The Significance of Thorough Welding Inspection in Industrial Applications
In the world of commercial applications, the relevance of thorough welding inspection can not be overemphasized. It plays an important duty in making sure the structural integrity and longevity of bonded parts. Advanced non-destructive screening methods enable for the early detection of potential issues, such as splits and insufficient blend, which, if left unchecked, can bring about devastating failures. Adherence to stringent industry criteria not just guarantees top quality but also constructs client confidence. As we check out the complex advantages of persistent welding examinations, one have to think about the broader effects on safety and security, integrity, and cost-effectiveness in industrial operations.
Enhancing Architectural Stability
When it comes to welding inspection in commercial applications, improving architectural honesty is vital. The primary objective of welding examination is to make sure that the welds are qualified of bearing the anticipated tons and stress and anxieties they will certainly encounter in solution.
The significance of maintaining structural integrity in bonded frameworks can not be overstated. Inadequately carried out welds can cause catastrophic failings, leading to costly repair work, downtime, and even endangerment of human lives. Examiners play an essential function in the lifecycle of commercial parts, giving assurance that the welding process provides the preferred strength and resilience.
Additionally, advanced technologies, such as phased range ultrasonic testing and digital radiography, deal boosted abilities in spotting possible weak points, permitting for corrective actions before concerns intensify. By focusing on the stability of welds via precise assessment, markets can make certain functional effectiveness and prolong the long life of their facilities.
Identifying Welding Flaws
Determining welding problems is a vital aspect of guaranteeing the safety and security and reliability of bonded structures. Common welding issues include porosity, fractures, incomplete blend, and undercutting.
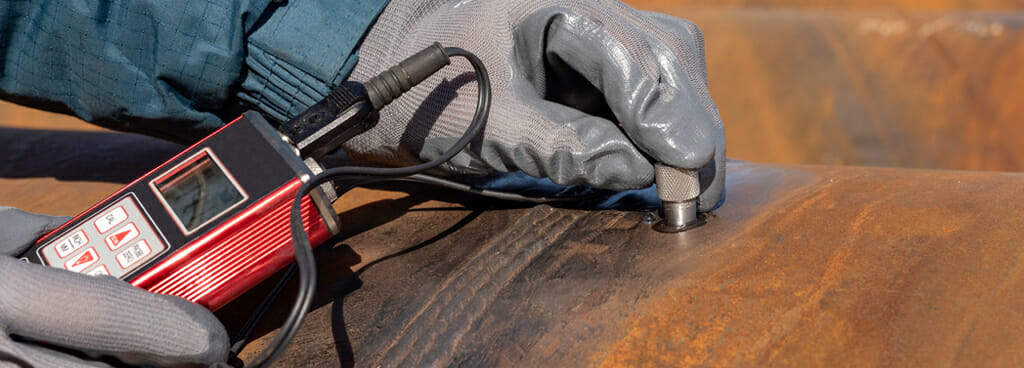
Competent examiners use both aesthetic assessment and advanced non-destructive testing (NDT) approaches, such as radiographic or ultrasonic testing, to find these issues. The prompt identification and rectification of welding issues are essential to keep the structural stability and longevity of industrial parts.
Making Sure Compliance Requirements
Conformity with well-known criteria, such as those offered by the American Welding Society (AWS) and the International Organization for Standardization (ISO), guarantees that welds meet minimum safety and high quality needs. These requirements incorporate a wide array of requirements, consisting of product requirements, welding procedures, and certification of welders.
Routine audits and evaluations are vital in confirming conformity. Assessors need to have a comprehensive understanding of the appropriate criteria and be adept at utilizing different non-destructive testing (NDT) approaches to evaluate weld high quality. By ensuring that welding techniques straighten with conformity criteria, business minimize the threat of non-conformity, which can Learn More lead to lawful responsibilities and security risks.
In addition, keeping compliance not just safeguards structural honesty but additionally improves a company's online reputation in the market. Customers and stakeholders are more probable to trust companies that constantly show a commitment to top quality and safety and security through strenuous conformity. Thus, making sure compliance standards is an important part in the effective application of welding in commercial applications.
Lowering Upkeep Expenses
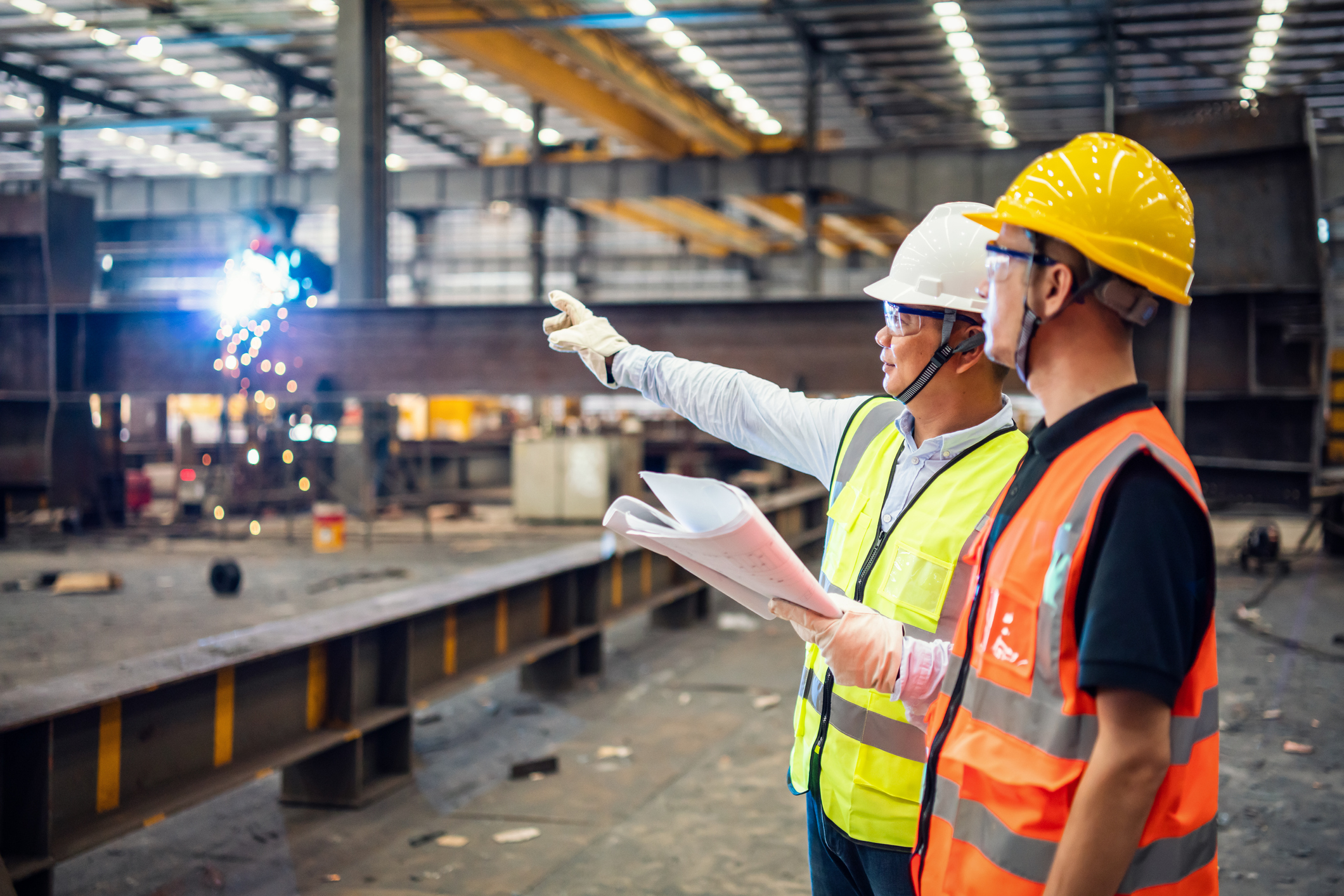
The application of advanced non-destructive screening (NDT) techniques, including ultrasonic, radiographic, and magnetic fragment evaluations, improves the ability to identify subsurface problems without compromising the architectural stability of parts. By employing these techniques, sectors can considerably expand the service life of their devices, minimizing downtime and the connected monetary concern of upkeep tasks.
Moreover, a robust welding inspection program supports the optimization of maintenance routines, moving from responsive to predictive maintenance strategies. This proactive method not only cuts unanticipated failings yet additionally enhances source allocation, ensuring that maintenance efforts are focused and efficient. Eventually, the financial investment in extensive welding evaluation is countered by the significant cost savings recognized with reduced upkeep demands, contributing favorably to the general functional efficiency of industrial ventures.
Improving Precaution
Although safety is a critical concern in industrial operations, accomplishing optimum safety criteria needs a devoted focus on the high quality and dependability of bonded structures. Welding inspection plays a critical duty in this context, as it makes certain that all connections and joints satisfy stringent safety requirements. Comprehensive inspections help identify issues such as fractures, porosity, or incomplete fusion that might compromise architectural stability. Such issues, if left unaddressed, present considerable risks, potentially leading to tragic failures.
To boost security procedures, embracing sophisticated non-destructive testing (NDT) strategies is essential. Techniques like ultrasonic testing, radiographic screening, and magnetic bit inspection permit for thorough examination without harming the framework. These innovations make it possible for examiners to spot covert imperfections early in the building process, promoting timely restorative actions. Carrying out a robust top quality control system that includes regular training for assessors and welders guarantees adherence to developed security requirements.
Lastly, promoting a culture of security within the organization highlights the importance of comprehensive welding assessments. Encouraging open interaction and collaboration among inspectors, welders, and designers adds to a description shared commitment to safety excellence. Welding Inspection Madison. In doing so, industries can secure their procedures, safeguard employees, and keep public depend on

Final Thought
Detailed welding assessment is crucial in industrial applications, considerably boosting architectural stability and reliability. By using advanced non-destructive testing methods, potential welding flaws such as splits and incomplete blend are determined early, making certain conformity with industry requirements and cultivating client count on. Extensive evaluations bring about reduced upkeep costs and contribute to a safer working atmosphere. Ultimately, the attentive implementation of welding evaluations plays a crucial duty in maintaining operational efficiency and safety in commercial settings.
As we check out the complex advantages of persistent welding examinations, one have to take into consideration the broader implications on safety, reliability, and cost-effectiveness in commercial operations.
The primary goal of welding inspection is to make certain that the welds are capable of birthing the expected loads visit this site right here and stress and anxieties they will experience in service. Efficient welding evaluation plays an essential duty in minimizing these expenses by making sure the stability and long life of welds, consequently reducing the risk of premature failings.Complete welding examination is indispensable in industrial applications, significantly boosting architectural integrity and reliability. Ultimately, the diligent execution of welding inspections plays a crucial duty in keeping operational performance and safety and security in industrial settings.
Comments on “The Duty of Innovation in Modern Welding Inspection Madison Practices”